Paper Based, Degradable films an recycling of films in packaging industry
Trends and Opportunities in Indian Packaging Industry:
Packaging is among the high growth industries in India and developing @ 15-20% per annum. In India, the fastest growing packaging segments are laminates and flexible packaging.
The growth of the Indian packaging industry will be heavily influenced by changing demographics such as growing urbanization and the rising proportion of middle class consumers. These changes drive the need for new packaging formats, such as different sizes, materials, and strength. In addition, innovations in the packaging industry, such as the development of lighter packaging with better barrier properties, add to the growth of packaging industry in terms of packaging material. The value of packaging consumption in India amounted to INR 811.1 billion ($15.2 billion) in 2012 which is projected to grow @ INR1488.6 billion ($27.7 billion) by 2018.
However, this growth also has a downside. Increasing use of plastics has also increased non degradable waste and it is taking its toll on nature. Currently, India is generating 56 lakh tonnes of plastic waste annually and India's contribution to plastic dump into the world's oceans is 60%.
This newly arising threat is demanding more use of paper based degradable films & recyclable films for packaging, and increase in the recycling of flexible packaging films.
Paper-based Films: Also called as Paper Laminates, these are coated or uncoated papers based on kraft and sulfite pulp. They can be laminated with plastic or aluminum to improve various properties. However, lamination substantially increases the cost of paper. Laminated paper is used to package dried products such as soups, herbs, pharma products and spices.
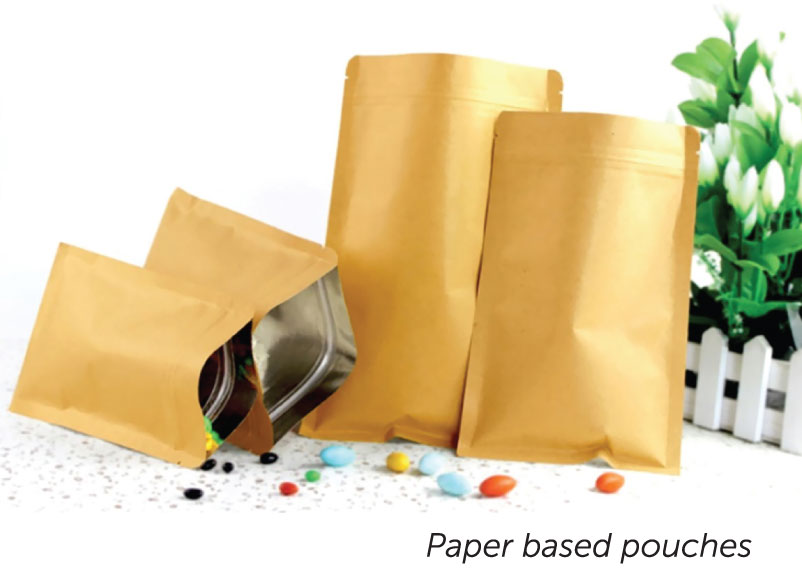
Biodegradable Films: Natural polymers derived from agricultural products (such as starch, proteins, cellulose and plant oils) are the major resource for developing renewable and biodegradable polymer materials (also called as bioplastics). Their raw materials mainly include Corn kernels, Bamboo, Plant fibres, Wood fibres, Mushroom, etc.
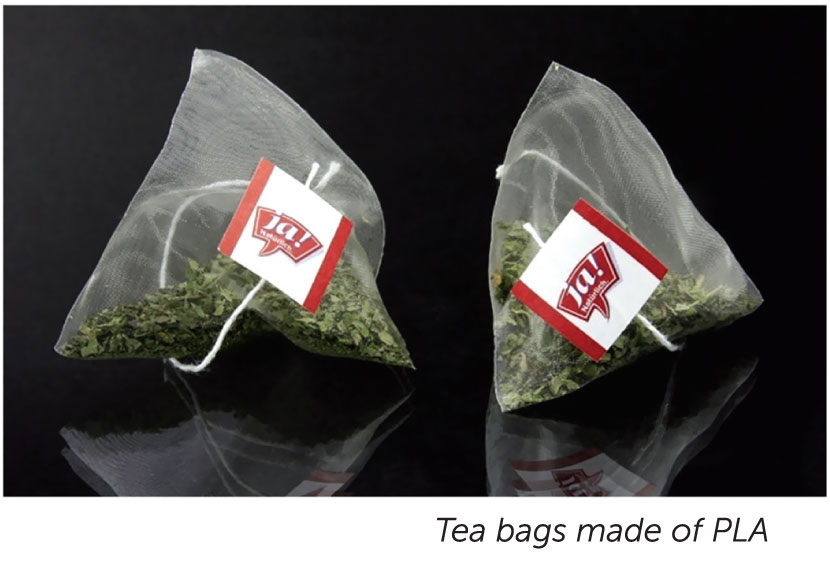
Four main types of Bioplastics are as follows:
- Bio-based polymers: Made from bio-based resources which may be extracted directly from plants (starch, cellulose) or produced by microorganisms in fermentative processes (e.g. polyhydroxyalkanoates
- Biodegradable plastics: Made from both natural and fossil resources and are biodegraded by microorganisms in their natural environment.
- Oxo-Biodegradable plastics: Mainly composed of polyolefins such as polyethylene (PE) and polypropylene (PP), which contain further chemical additives intended to accelerate degradation.
- Bio-nanocomposites: These are biopolymers which have been stabilized using nanoparticles. The nanoparticles enhance technical properties, such as barrier, thermal, chemical or mechanical stability and include nanoclays and nanosilver.
Vendors are introducing biodegradable and sustainable forms of packaging to cater to the growing demand for eco-friendly packaging products. The Coca Cola Company launched its Plant Bottle, which is partially made from bio-based plastics, while Danone is using PLA for its yoghurt cups.
Polymer-based Multilayer Films: Currently these are the most commonly used packaging materials in packaging industry. Multilayer films are used in packaging to achieve specific performance requirements in a cost effective manner. Multilayer film fabrication process allows selection of polymers and important film properties, including barrier, mechanical, sealing, adhesion and shelf appearance to design flexible packaging to meet application needs. According to the Flexible Packaging Association (FPA), the flexible standup pouch product to package ratio is 35 times greater than that of glass bottles with metal caps and 21 times greater than the aluminum can. This allows for more product to be shipped using much less packaging. Included in the Association's statistics is the fact that flexible packaging uses 50% less energy to produce and 60% less plastic than rigid bottles.
However, its recycling is equally difficult. While sustainable packaging is a great talking point for the flexible packaging sector, there is still progress to be made to be entirely environmentally responsible.
Flexible packaging recycling today
As it stands, there is no proper closed-loop system put in place to handle the recycling of flexible packaging, especially multi-layer high-barrier materials, specifically structures composed of aluminum foil within a polyethylene (PE) laminate. Mono-layered packaging is more easily recyclable because it doesn't contain the aluminum foil center. But the process to recycle multi-layered flexible PE packaging involves more steps than the traditional plastic recycling regimen by including separation of each layer.
Since a lot of flexible packaging is used for food products, another hurdle for recycling is food contamination.
There are great initiatives in the works from forward-thinking groups like the Flexible Packaging Association, who has a strong focus on sustainable packaging. The FPA is working with several producers for packaging that is safe for the environment. The Sustainable Plastic Coalition, the Association of Postconsumer Plastic Recyclers (APPR); and The Flexible Film Recycling Group (FFRG), are also promoting and increasing public education and outreach on plastic film recycling.
Cradle-to-cradle design is another initiative that organizations such as Enval are working toward. The philosophy of cradle-to-cradle design is to keep packaging products within the reusable system without downgrading or becoming 100% waste. Enval has found a way to fully recycle the aluminum foil between the layers of polymer laminate and keep it clean. Along with that, they can produce oils and gases from the plastic components, which can be used for electricity and heat. This is possible by using microwave-induced pyrolysis, which is not possible by incineration because of the inclusion of oxygen in the process.
Manufacturers are also moving toward the cradle-to-cradle concept by implementing the use of either eco-friendly materials that biodegrade, bio-based plastics that may also be biodegradable or techno-friendly materials that can be recycled without being down-cycled into low-grade materials. Using plant-based materials in flexible packaging would mean economic growth for agricultural industries. It would also push further agricultural development due to demand for crop growth.
Possible optimization of flex pack recycling:
While Enval's process is currently the best solution for handling of multi-layered packaging waste, there is no solution to adequately recycle the plastic components into other plastic materials.
With pyrolysis, char residue formed from plastics contains inorganic materials, 80% liquid carbon and 20% carbon gas (CO2 gases are not created because of lack of oxygen in the chamber). The carbon can be transported to different locations for liquid fuel/energy needs. The ash can be used as ingredient in products such as concrete ready mixes. While the carbon can be used as fuel, companies tend to enter mixed waste materials into the pyrolysis chamber, producing fuel that may not have optimal usability.
What needs to continually be researched is an effective way to turn this carbon liquid fuel into a more serviceable, high-integrity energy source.
Developing more effective end-of-life processes (especially within pyrolysis) for flexible packaging; to have an even lesser impact on the environment is a challenging quest, but it is possible. With the innovations the flexible packaging sector has already made, like using bio-based material, or the waste-to-energy process of pyrolysis, the building blocks of further development have been set in place.
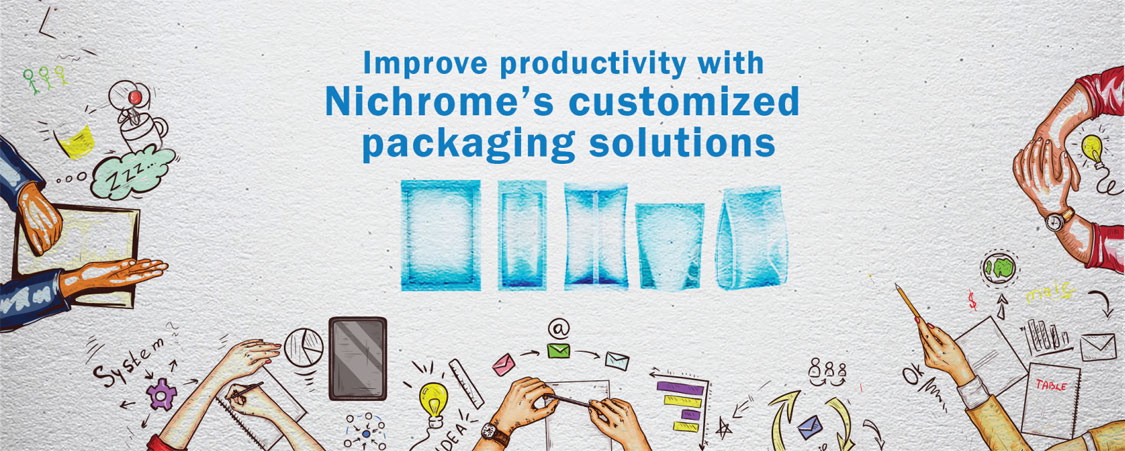
Food
- Snacks & Namkeen Packaging Machine
- Ready-to-Eat Food Packaging Machine
- Grains & Seeds Packaging Machine
- Milk & liquids Packaging Machine
- Powder Packaging Machine
- Spice Packaging Machine
- Coffee Packaging Machine
- Sugar Packaging Machine
- Oil Packaging Machine
- Salt Packaging Machine
- Tea Packaging Machine